This equipment focus will feature APT's RDGK alluvial and hard rock mining plant, a small scale mining solution incorporated within APT's GroundBreaker range.
"I have worked with a team to make the RDGK15 into a very competent gold recovery pilot plant. The gold recovery plant is highly portable and was run as a product/pilot plant. The percentage recovery of gold was greater than suggested from constant supervision of the RDGK15 hard rock and concentrator combo unit. The simplicity of the GoldKacha concentrator makes it a very easy unit to achieve regular good percentage gold recoveries." - APT client, Zimbabwe
In a nutshell, the RDGK is a complete hard rock gravity recovery solution, combining the APT impact crusher and GoldKacha concentrator in one neat, modular package. In keeping with APT's philosophy, the RDGK has been designed in such a way that you can add onto the individual components as you grow or as your resource requires. As such, there are several variations available depending on your requirements and affordability. Below are some of those versions including the Goldilox, incorporating the gold storage box, and the RDGK trailer plant for optimal mobility. If you have any questions, comments or concerns, we are always here to hear them so feel free to email us on info@aptprocessing.com or contact us here.
Below is the diesel powered RD15 Impact Crusher, with a capacity of 1.5 tonnes per hour. Completed and ready for shipment. As you will see, it has been designed such that the GoldKacha can be fitted beneath the crusher should the need arise. The GoldKacha has a capacity of up to 3 tonnes per hour.
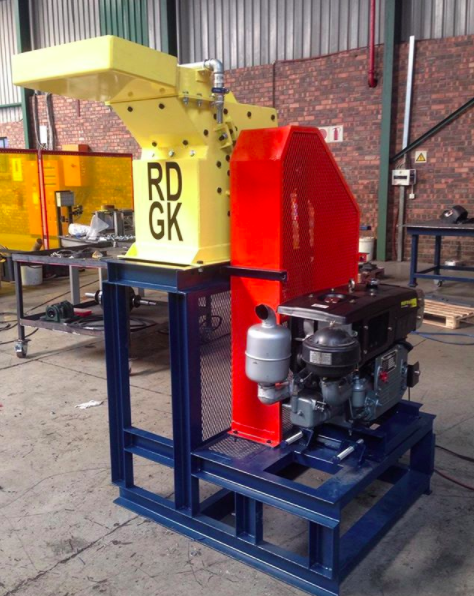
Below is an RDGK with automated and secure Goldilox™ system. A dry run is always completed before any plant heads out to site, with this one in particular heading off to it's new home in Southern Africa. The Goldilox™ system ensures there is no access to the concentrates generated during the run cycle. All concentrates are automatically discharged at pre-set intervals into a locked concentrate box sitting beneath the GoldKacha. The security cage and concentrates box are unlocked at end of day and the concentrate box is taken to a secure area for upgrading and smelting of the cons. The run time interval is pre-set by the mine operator and password protected. Goldilox™ also logs run time to allow owners and operators to see a record of daily use and total use. Combined with APT’s alluvial and hard rock plants, small scale miners are now able to run a secure operation on a start-up budget with the peace of mind, knowing gold recovered remains yours.
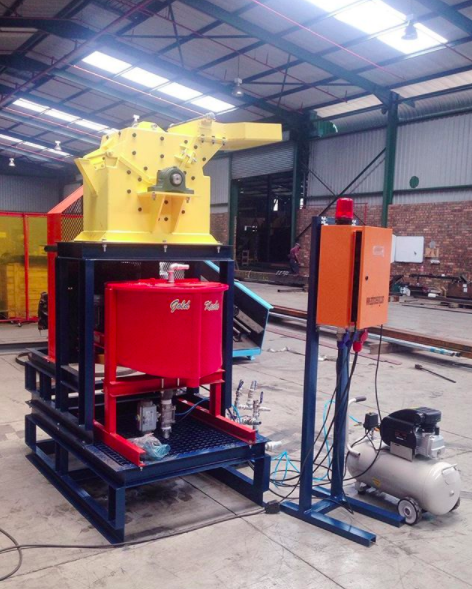
Below, manufacture and pre-assembly is complete on APT's 1.5tph hard rock and spirals processing plant, built in a record time of just 6 weeks.
Here is a video of our trailer version of the RDGK, showing exactly how it operates.
[embed]https://www.youtube.com/watch?v=63tHE3pIZ1s[/embed]
Last but certainly not least is some outstanding gold product processed using the APT RDGK15 plant, with the GoldKonka for upgrade. The RDGK15 is one of our smallest hard rock processing plants, and boasts the perfect balance between simplicity and efficiency.


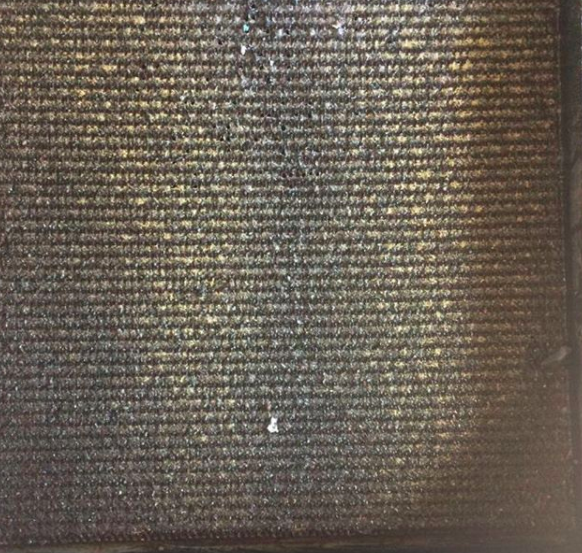